Enhancing Cabin Comfort
TotalSim Uses STAR-CCM+ and Advanced Thermal Management Techniques in NextGen NASCAR Vehicles
The Situation:
NASCAR’s introduction in 2022 of the NextGen model race car was a large-scale platform update with the goal of modernizing the design, build and operation of their top level Cup cars. With any new car design comes new challenges, especially when moving to such a complete design overhaul. One major challenge that cropped up was maneuvering from an open under floor design to a closed flat floor design as there was significantly less cooling air flowing to the driver cabin.
Client Challenge:
While NASCAR continued to make the car and cabin cooling more robust by making changes, which included:
- A windscreen vent for driver cooling
- Rear window cooling slots
- An underfloor driveshaft tunnel cooling duct
- Floor cutouts
- Wheel tub cutouts
they also wanted to further reduce cabin temperatures. During 2023, they had another major idea of introducing a short exhaust in order to remove a portion of the large heat source sitting next to the race car cabin; however, this idea would need to be tested to see if the major change (and costs) were justified prior to the 2024 season.
Type of TotalSim Engagement:
NASCAR has worked with TotalSim in the past and knew that we could help tackle the thermal management challenges that had appeared in the NextGen design.
What TotalSim Did:
TotalSim began by running simulations at a low vehicle speed to mimic a street circuit. Its typical slower speeds and heavy braking would represent the ‘worst case’ scenario for cooling that the cars see all season. The runs were set at a slow corner entry braking configuration using a full model of the racecar that included over 11 different solid material types; modeling hundreds of solid parts in the car such as:
- Exhaust assembly including inconel, stainless steel and insulation mats
- Reflective films for thermal radiation management
- Carbon fiber panels and their core materials
- Stainless steel and mild steel for frame components
- Foam blocks used for crash protection materials around door panels
All the components were included to accurately track the conductive heat transfer through varying materials, the conjugate and convective heat transfer from the solids to the air and the radiative heat from the very hot exhaust and engine to other components of the vehicle.
Prior to the simulation, NASCAR was able to collect Forward Looking Infrared (FLIR) data from a track test that was used to correlate and validate the simulations. Almost identical hotspots were shown between the FLIR track data and the simulation baseline data. This gave TotalSim and NASCAR the confidence to move forward with modeling the new concepts
Once all of the data had been collected, and the baseline had been completed and validated, TotalSim began testing NASCAR ideas and concepts to increase cabin comfort for NASCAR drivers. The car already had cooling air supplied directly to the original exhaust design but due to the muffler’s position, much of the cooling air flow would recirculate the exhaust heat back into the engine bay. This left an inadequately cooled exhaust pipe right next to the steel chassis structure which then in turn, conducted that heat into the cabin.
To combat this, NASCAR created a short exhaust design which carried a shorter muffler and exited earlier on the car. The panels around the short exhaust were redesigned to increase the air volume around the exhaust and muffler to better allow the cooling air to convect heat away. The chassis was further protected by an additional sealing panel that was used to prevent hot air from propagating down the chassis sides.
All of these options were created first in CAD, and then modeled in CFD simulations. Each part or design option was able to be tested and quantified by monitoring the temperatures in the critical cabin areas. The short exhaust design simulations showed that it was able to accomplish much of the cooling desired. NASCAR and TotalSim also tested several additional design options that could be added or track tested in the future as needed.
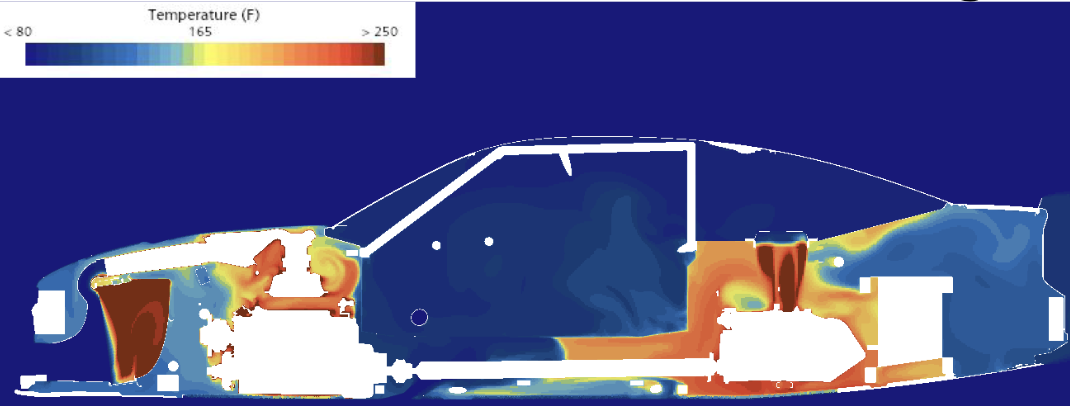
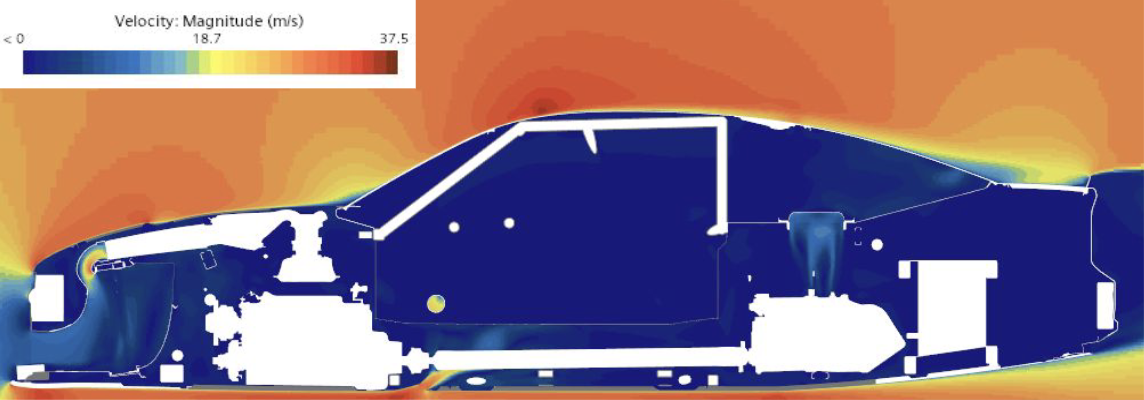
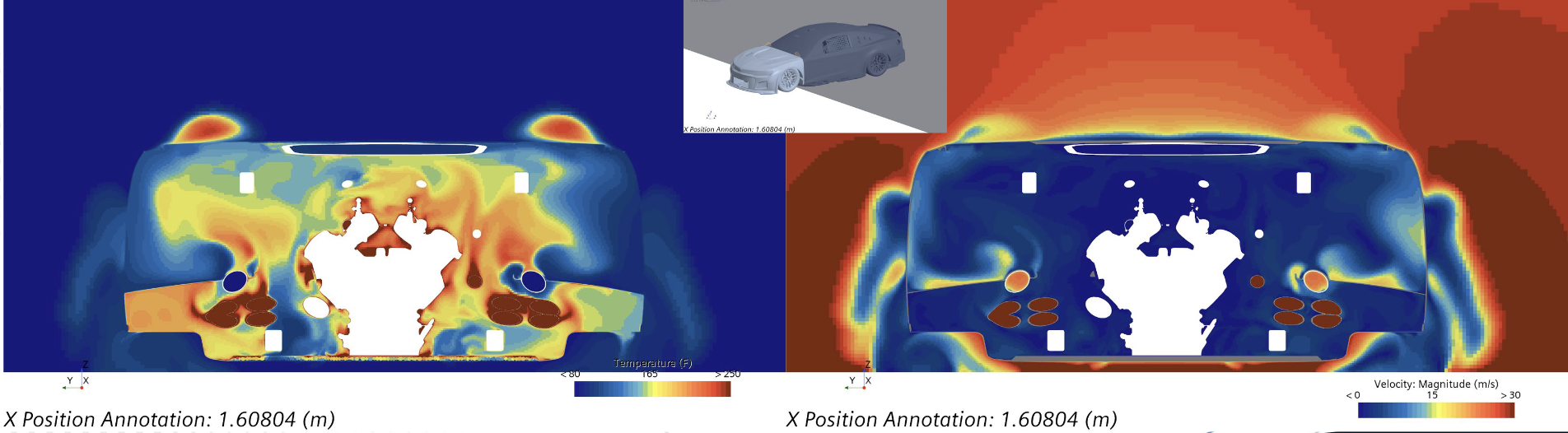
Results:
Through the power of STAR-CCM+ CFD simulations, conduction, convection and radiative heat transfer were successfully accounted for on a full car model of the NextGen race car. The simulation results provided NASCAR the confidence to build a prototype short exhaust system and other modifications and take those to perform on-track tests with several teams and drivers. The prototype testing matched the gains seen in the simulation results and enabled NASCAR to update the NexGen race car specification to the new designs. TotalSim’s simulation and analysis work leveraging the power of STAR-CCM+ allowed NASCAR to find a solution for the cooling challenges swiftly and cost effectively. The effective use of modeling and simulation reduced the need for multiple prototypes and repeated physical testing, which fits well with the rapid design cycle and short off-seasons in NASCAR racing. CFD simulations also provided deeper insight into the root causes of the issues. As a result, this short exhaust system evaluated during this project helped solve the cabin comfort challenges and is still used today on all 40+ cars competing throughout the NASCAR season.
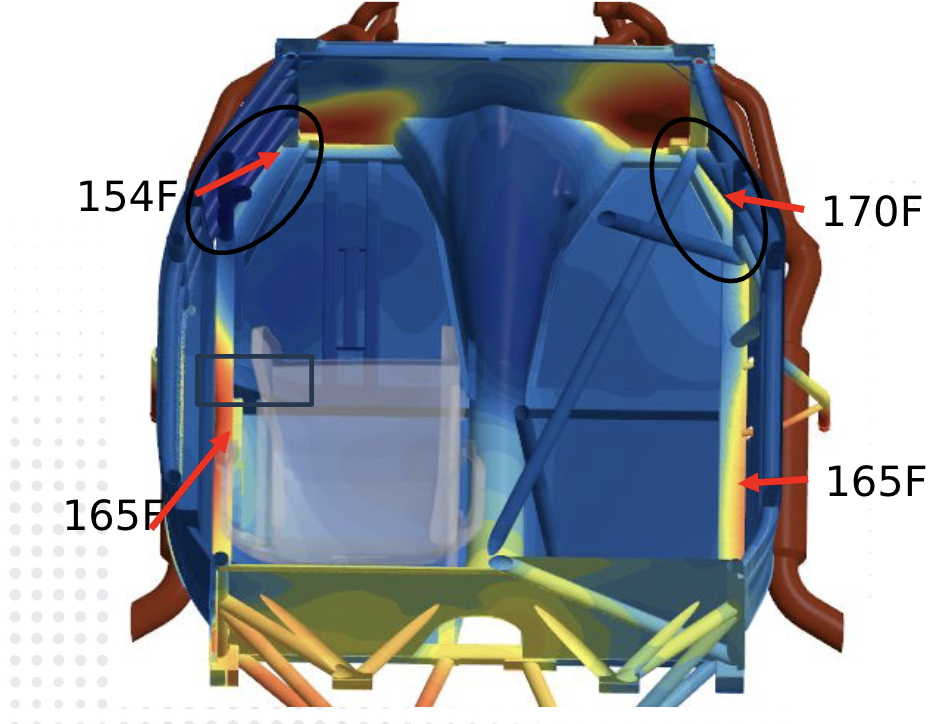
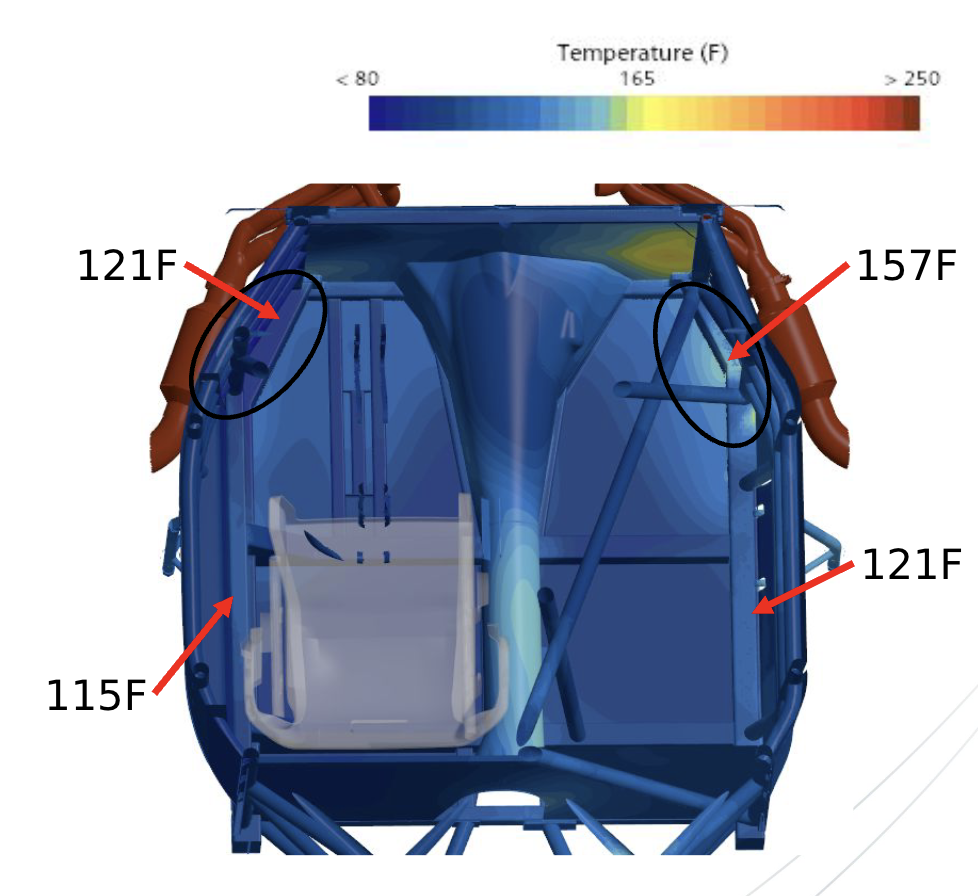
Similar Work:
Learn more about the ways TotalSim can help you overcome your aerodynamic challenges
*What is CFD?
Computational fluid dynamics (CFD) is a branch of fluid mechanics that uses computer numerical analysis and data structures to analyze and solve problems that involve fluid flows, typically solved on large supercomputers. Fluid mechanics plays a significant role in the engineering process when developing new designs. Analyzing the aerodynamic and thermal qualities of a product using experimentation is a well-established approach however experimentation can be costly, limiting, time-consuming, and difficult to execute especially on a large scale. Progression of computing power has allowed the field of CFD to prosper acting as a complement to physical testing and in some cases replacing it. CFD is the science of predicting fluid flow, heat transfer, mass transfer, chemical reactions, and other flow properties by solving governing fluid flow equations using numerical methods. Across the industry, CFD is routinely used to drive product development, troubleshoot issues, study and optimize new designs and concepts, and map performance. CFD methods are heavily used across many disciplines with motorsports being a leading proponent.